Stop window shake and rattle — but keep the roll
Proper window installation tips and tricks Story and Photos by Angelo Van Bogart Proper window and weatherstrip installation will leave the “shake, rattle and roll” to your car’s radio and…
Proper window installation tips and tricks
Story and Photos by Angelo Van Bogart
Proper window and weatherstrip installation will leave the “shake, rattle and roll” to your car’s radio and Highway Hi-Fi, not its window glass.
Annoying window glass rattles and leaky weatherstrip can hinder enjoyment behind the wheel of a vintage car or truck, and no one knows that more than Jerry Kopecky of Kopecky’s Klassics. In his restorations, which frequently focus on finned MoPars, Kopecky takes great pains to correctly install the weatherstrip and glass of his own cars and his customers’ cars in the factory manner. This not only prevents the aggravation of wind noise, water leaks and window rattle, it also ensures smooth, proper operation with a factory appearance for the show field.
The bulk of Kopecky’s restorations are complete body-off-frame rebuilds, but the steps to install and adjust the window components will also work on a partial restoration of most 1950s and ’60s cars from many manufacturers. In a complete restoration, Kopecky strongly recommends installing the windows and associated hardware with new and/or rebuilt components while the car is apart and without an interior. This will reduce the potential for scratching and chipping a fresh paint job by tearing back into the components at a later date.
The subject car in this story is a 1960 Chrysler 300-F convertible, but the process is similar for restoring many postwar vehicles. Likewise, the part sources mentioned below can service many different types of vehicles.
Window mechanisms
To re-install the windows and associated components correctly, begin by photographing them in the car during disassembly. Remove the glass, associated trim, window channels, vent windows and frames, switches or handles, etc. Label these parts and hardware so they can be correctly reinstalled. This advice is good for any step of the tear down and rebuild of a vehicle and its parts.
Kopecky begins by cleaning parts he will restore in a parts washer. (The units pictured here were free of corrosion and did not require media blasting and re-plating.) Once these parts are clean and free of grease, dirt and sand, they can be inspected for wear, breaks or other problems that will prevent them from functioning properly. Now is also the time to replace any defective parts.
Parts that Kopecky does not personally restore, such as the power window motors and switches, are sent to J.C. Auto Restoration and rebuilt with new brushes, gears, etc. Even if the switches and motors work, Kopecky strongly recommends rebuilding them while they are out of the car to ensure many more decades of performance.
When reassembling the window mechanisms, Kopecky lubricates the moving parts with white lithium grease since that is what the factory used. He uses a spray-on lithium grease to get in all the crevices between the brackets and the gears. Well-lubricated parts help prevent the “two-hand window roll-up” by allowing the windows to roll-up freely. He also re-installs original-type rubber or leather washers that were used by the factory. These 50-cent parts are one of the main components missing in a loose-fitting mechanism, and can be the source of a loose-fitting window that rattles.
Window channels
The window channels are essentially made up of U-shaped channels in which the glass rests or is directed, the weatherstrip that goes in that channel, and the hardware that fastens the channel to the vehicle’s body. All of these parts are cleaned and media blasted to remove foreign matter, such as rust and old adhesive from the channel. Note the original shape and type of weatherstrip used on the channel before disassembly it in order to match new material to the original-type material.
In this application, Kopecky noted the replacement window channel weatherstrip supplied by the marque-specialist vendor was not of the correct shape or thickness. Since this weatherstrip was too thick, it may bind the window and make it difficult to smoothly raise and lower the window glass once installed. For the correct window channel weatherstrip, original-type material was located in Restoration Supply Co.’s catalog and ordered in bulk, then cut to size. For this 1960 Chrysler, the correct material is a mohair product that looks somewhat like Velcro, but is not as thick or abrasive to the touch.
To install the new window channel weatherstrip, Kopecky lays the new weatherstrip in the clean channel to determine how much will be necessary. He measures the length and width of required mohair, adding an extra quarter inch or more of mohair to each end of the channel. This extra weatherstrip will ensure the glass does not make contact with the metal channel, which could scratch or chip the glass.
So that the weatherstrip lays as flat as possible in the channel, Kopecky wedges a piece of bar stock in the channel to press the weatherstrip as flat and flush with the channel as possible. Without the bar stock, the weatherstrip is likely to lay in the channel with a U shape, which may bind the window during operation. Once he is happy with the fit of the weatherstrip in the channel, he applied 3M Super Weatherstrip & Gasket Adhesive to the back of the weatherstrip and in the channel, then laid the weatherstrip in the channel, using the bar stock to hold the weatherstrip in place, tightly in the channel. Once the adhesive on the weatherstrip dries, the channels are placed on the bench until they can be installed with the other components.
Door and rear window sweeps
At the top lip of each door channel, where the window slides into the door, and at the body, where each quarter window slides into the rear fender, is a fuzzy window sweep with a stainless steel backing. This piece of weatherstrip prevents the window from scraping against the body and also functions as a seal to keep water from entering the body, and although small, is a very important piece.
As a restorer, Kopecky often examines this piece of weatherstrip on restored cars, particularly noting how it has been attached. In the case of this Chrysler, the weatherstrip is attached at the back of the piece with clips, but many times, a restorer will rivet this piece of weatherstrip to the car. Kopecky recommends against rivets, not only because it isn’t factory correct, but also because the rivet heads can scratch the glass as the weatherstrip ages.
The original window sweep clips on this car were weathered but present, however, Kopecky was able to purchase new clips from a marque-specific vendor. If not available, the originals would have been restored. New window sweep weatherstrip was obtained from Restoration Supply Co. in bulk after matching the original style to products the company offered.
Since the new window sweep weatherstrip was ordered in bulk, it had to be cut to length using a Dremel tool with a small grinder. To match the factory design of the sweep weatherstrip, of which the end was bent at a 90-degree angle, Kopecky made a pie cut at a 45-degree angle in the stainless to bend the end of the stainless-backed sweep at a 90-degree angle, simliar to how the factory made the part. After window sweep pieces were cut to length for each door top and quarter window opening in each rear fender, they were fastened to the body with the original-style clips.
Door vent windows
In this complete restoration, the door vent windows were completely removed from the frames, which were themselves completely disassembled so the pot metal pieces could be plated and the stainless parts polished. Since plating can cause the pot metal parts to become thicker than they originally were, the available reproduction rubber parts may require trimming to fit.
After several test fits with the window frame out of the car, Kopecky determined how much thickness had to be removed from the rubber in order to make the vent window gaskets fit in the the vent window channel. He trimmed the rubber with an Exact-O knife, and once it was ready to install, lubricated the rubber gasket with dish soap and water to slide it into the channel. A putty knife was used to position the gasket in place, and the smooth end of a 90-degree screwdriver-size hook tool was used to press the gasket all the way into the channel. On most vehicles, this gasket will lock into the channel. Kopecky was careful not to cut or scrape the gasket while using the tools to position the gasket in the correct place.
While the vent window frame is off the car, Kopecky reassembles the unit and also makes any adjustments to the window lock and tensioner. The spring for the vent window lock will be dry and require lubrication with spray-on lithium grease
Installing the windows
Once the window, gasket and any adjustments to the spring and other hardware are completed on the door vent window assembly, it’s ready to be installed on the car. Kopecky works from front to back when installing the glass, first fitting the vent window frame about 80 percent on the car. The vent window assembly is left slightly loose so it can be adjusted after the door and quarter window are installed. He also aligns the vent window assembly parallel to the windshield frame.
The door window mechanism, glass and window channel are installed second as Kopecky works from front to back on each side of the car. The window mechanism is likewise 80 percent installed so it can be tweaked after the quarter window is installed with its window mechanism and associated channel.
With all of the glass in place, the convertible top is raised to provide a horizontal line to serve as a guide when aligning the top of each window frame evenly to the car. The windows are not made to fit snugly against the top frame, as space needs to be left on a convertible for the top fabric and top weatherstrip. (On a closed car, the roof will serve as a guide.)
Now, each window can be adjusted so it is flush, even and at the same angle as the window next to it when raised. This process requires tightening and loosening the bolts that hold each window mechanism and the vent window assembly to the body. As tedious as this may be, it’s required to get a good fit and prevent leaks between windows on a convertible or hardtop, as well as a flush and almost seamless transition from window to window.
Once all the window mechanisms are completely tightened, the window stops for each window can be installed.
While the door panels are off, check the operation of the windows to make sure they do not bind and all the motors and switches in a power window-equipped vehicle work properly. Also make sure the wiring is not caught in any parts and is in a safe place, away from edges that may cut it or moving parts may pinch the wiring. If everything is ready to go, put the panels on the car and listen to the shake, rattle and roll coming from the radio, not the car.
Sources
- Kopecky's Klassics: 715-445-4791
- JC Auto Restoration: 425-672-8324, www.jcauto.com
- Restoration Supply Co.: 800-306-7008, www.restorationstuff.com
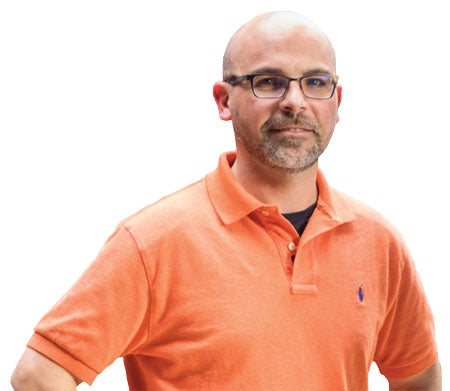
Angelo Van Bogart is the editor of Old Cars magazine and wrote the column "Hot Wheels Hunting" for Toy Cars & Models magazine for several years. He has authored several books including "Hot Wheels 40 Years," "Hot Wheels Classics: The Redline Era" and "Cadillac: 100 Years of Innovation." His 2023 book "Inside the Duesenberg SSJ" is his latest. He can be reached at avanbogart@aimmedia.com